Getting Started With Cut and Curl Candles
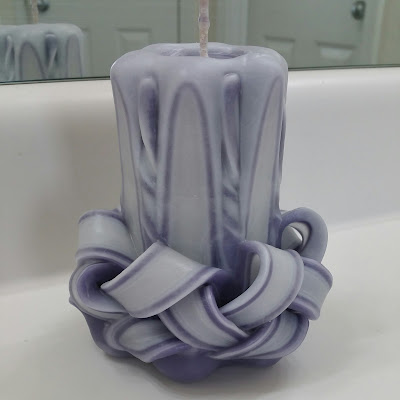
There's not a wealth of detailed instructions and technicalities on how to do these type of candles, unlike beading or cake decorating. What I did find though, were a ton of great YouTube videos showing the carving process. Unfortunately, that's not helpful when you are new to candle making and aren't sure what type of wax to use, what temperature the wax needs to be at when you start dipping, importance of heating the core, making a core candle, making/finding a proper sized wick, etc.
Throughout this series, I will hopefully help answer some common beginner's questions. I'd also like to share with you what I started with and some of the things I learned along the way. In this first post, I'll discuss what type of wax to look for, and from personal experience, what not to use.
In my search, I was able to find a couple of resources that helped uncovered some of the mystery. One Stop Candle has four wonderful tutorials on their process and carving instructions for different candle designs. Please also see his troubleshooting guide and supply list. My second resource was a purchase from eBay: Dana Brook's Cut and Carve Candles book. I will refer to the Google preview of her book throughout this post as it is accessible for everyone.
![]() |
January 11 |
The appropriate wax is probably one of the more important things to get right in the beginning. If you don't have the correct wax, that's money, time and frustration that could have been saved. I won't go into all the different types out there, as a internet little research will uncover a slew of helpful and detailed candle making websites.
There is a world of difference between waxes and some personal trial and error on this will have to be made. Start small, see what works and do some research. From personal experience for Cut and Curl candles, I'd stay away from regular craft store wax as they are geared more towards container and pillar candle making. Although I don't recommend it, I did have a tiny bit of luck with the Hobby Lobby Premium wax mixed with beeswax, but there's still a night and day difference between that, and what I am using now. The good stuff is usually cheaper too, if you can buy in bulk. Micheals pillar wax didn't work, as you can see from the photo. Now, I'm no expert. I'm sure there could be great products out there not labeled for it but may work well anyway.
You can find a good wax labeled for Cut and Carve online or locally; the closest place that sell supplies is over an hour from me, so it depends on your situation and location. Straight paraffin wax (meaning with no additives like vybar or stearic acid, just paraffin) will work also, according to One Stop Candle. The MP, or melt point is something to keep in mind when purchasing; you'll need wax with a melt point of around 135 degrees (see the Cut and Carve Candles preview) to no more than about 145 degrees. Dana mentions she uses a mix of two. Again, try to see what works for you.
I've listed a few places I found online that sell wax labeled as Cut and Curl or mentions it in the description. I have personally tried only the ProBlend 550 from the list and have commented any dealings I had with the rest. This is not an exhaustive list. You can do a search on Google for "Cut and Carve candle wax." These are just a few I came across in my research that seem to be used by others. Please note that I cannot guarantee the quality, trustworthiness of sites or particular results from some of these.
1. The Flaming Candle- ProBlend 550 MP 138-140. This is the one I use currently, and it works well. Shipping is the most reasonable for a 10 pound bag through USPS that I have found anywhere besides Aztec. I live an hour away, I so just pick up. It comes in granule form, so no breaking up slabs.
2. Aztec- IGI 1250 MP 140-143 and IGI 1245 Reasonably priced shipping for 5lb and 10lb increments through USPS. I think I remember them telling me over the phone that the 1245 was their more popular cut and carve wax, but you can call to confirm.
3. Candles and Supplies IGI 1240 MP 136. Purchased a star mold and some microcrystalline wax from them.
4. Bittercreek Candle Supply- IGI 1343 MP 138 Really good customer service from my brief experience.
5. Lone Star Candle Supply- IGI 1343 MP same as above
6. CandleScience- IGI 1343 MP same as above Has a good review about its cut and carve application.
7. Candlewic- 145 Melt Point Wax 4045EP MP 145.
If you are just getting started, I'd personally start with a small amount--5 to 10 pounds should work initially. You won't be able to do much with this, as you'll see later, but it'll give you an idea if it'll work for you. Once you find a good wax, then you can order a case of it to help save on shipping costs later.
This wraps up today's post. In the next part of the series, I'll discuss my minimal basic set up and supplies. Please feel free to add anything from your experience or something I've missed in the comments below. I hope this has been helpful!
Connect with me
No comments:
Post a Comment